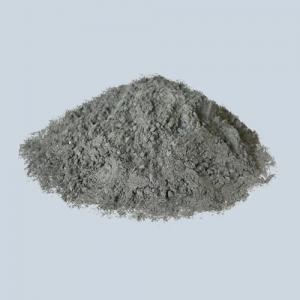
Add to Cart
Supply Low Price Furnace Liner Refractory Silica Ramming Mass For Construction Of Various Kilns Lining
Silica ramming mass is made of quartz (SiO2) refractory raw material as aggregate and a certain proportion of powder, binders and additives, which can be used?for construction of lining of various kilns. The silicon ramming mass introduced today is used in the working layer of the tundish, and the service life can be up to 30 hours after the overall casting, which is generally applicable to small and medium-sized tundish.
Advantages of Silica Ramming Mass
Physical and chemical index
Aluminum-magnesia ramming material, high-alumina (or corundum) – silicon carbide – carbon ramming material, alkali refractory ramming material and zirconium mullite ramming material.
Name | Composition | Application | Note |
Carbon packing material | Metallurgical coke powder (less than 4mm) 80% | The gap between blast furnace base clay brick masonry and furnace shell, blast furnace hearth, the gap between furnace hearth clay | Volume ratio |
Carbon ramming mass | Metallurgical coke powder (less than 4mm) 85% | Blast furnace lining | (mass ratio) |
Magnesia ramming mass | Magnesia sand (granularity ≤5mm) 85% | Lateral lifting open hearth furnace bottom | (Volume ratio) |
Magnesia sand 89%~91.5% | Electric furnace bottom | (mass ratio) | |
Magnesia sand 89% | Electric furnace bottom and ramp | Mass ratio | |
Chrome plastic refractory | Chromite 97% | Soaking pit hearth central part, burner nozzle surrounding | (mass ratio) |
Magnesia ramming mass | Magnesia sand 50% | Soaking pit hearth central part, burner nozzle surrounding | (mass ratio) |
Chrome oxide ramming mass | Chromite (granularity ≤3mm) 90% Iron oxide (granularity ≤3mm) 5% | Circular heating furnace bottom | (volume ratio)
|